Choosing the Right Mobile Jaw Crusher
Release time: 2025-03-14
Mobile jaw crushers are versatile, mobile crushing machines designed to break down rocks and construction materials on-site. They consist of a jaw crusher mounted on a portable chassis, equipped with tracks or wheels for mobility. In the aggregate, mining, and construction industries, mobile jaw crushers have become indispensable for their ability to move between locations and crush material directly at the source. This on-site crushing capability reduces the need for transporting raw materials to fixed plants, saving time and fuel. As a result, mobile jaw crushers play a critical role in modern production, offering flexible crushing solutions for everything from quarry rock to demolition debris.
As a leading mobile crusher manufacturer in China, Suhman has been at the forefront of this technology. Tracked mobile jaw crushers – a type of mobile crushing plant – exemplify how innovation in mobility and crushing power can streamline operations. In the following sections, we provide a structured analysis of mobile jaw crushers, covering their working mechanism, types (crawler vs. wheeled), efficiency, specifications, costs, applications, environmental impact, integration with other equipment, and tips for selecting the right model.
How Mobile Jaw Crushers Work
Mobile jaw crushers operate on the same principle as stationary jaw crushers but with added mobility. At the core of the machine is the jaw crushing unit – a heavy-duty jaw crusher consisting of a fixed jaw and a moving jaw. Material fed into the crusher is compressed between these jaws and broken into smaller pieces. The crushed material then exits through a discharge opening, adjustable to control output size. This jaw mechanism provides high reduction ratios, making mobile jaw crushers ideal for primary crushing of large rocks and materials.
Key components of a mobile jaw crusher include:
- Jaw Crusher System: The main crushing mechanism, usually a robust jaw crusher powered by either a diesel engine or electric motor. It handles the brute force of crushing, with models designed for various hardness (from soft concrete to hard granite).
- Power & Transmission: Mobile jaw crushers are typically powered by diesel engines that drive the crusher and auxiliary systems. Modern units often use diesel-hydraulic or diesel-electric configurations. In diesel-hydraulic systems, the engine drives hydraulic pumps that power the crusher and tracks. In diesel-electric designs, the engine powers a generator that drives electric motors for the crusher and travel system. This setup can improve efficiency and may allow dual power (either diesel or plug-in electric) for flexible operation.
- Mobility Chassis: Depending on design, the crusher is mounted on a tracked chassis (crawler-type) or a wheeled chassis. The chassis includes suspension or track frames and travel motors, enabling the entire unit to move. Crawler tracks provide self-propelled movement and stability on rough terrain, while wheeled frames (often with axle steering) allow the unit to be towed or semi-mobile.
- Feed Hopper and Conveyor: Mobile jaw crushers integrate hoppers and vibrating feeders to regulate material flow into the jaw. After crushing, a main discharge conveyor transports the processed material out of the crusher. This conveyor can often be adjusted in height to discharge into piles or secondary crushers. Some models also include side conveyors for removing fines or a pre-screen to separate smaller material before crushing.
- Control System: An onboard control panel (sometimes remote-controlled) allows the operator to start/stop the crusher, control feeder speed, and maneuver the unit. Safety systems are built-in to stop feeding or shut down the crusher if overloaded or in case of engine/temperature warnings.
Crawler vs. Wheeled Models: Mobile jaw crushers come in two primary mobility variations:
- Crawler-type mobile jaw crushers use caterpillar tracks for movement. They are fully self-contained and can crawl around the job site under their own power.
- Wheeled mobile jaw crushers are mounted on wheels (often as a two-axle or three-axle trailer units). They are portable but generally require a separate vehicle (like a truck or tractor) to move them between sites or within a site. Some wheeled units have small onboard engines or can hook up to external power for the crusher, while relying on towing for relocation.
In operation, a mobile jaw crusher is brought to the material site, set up using its hydraulic supports or parking brakes, and begins crushing with minimal installation. This contrasts with stationary jaw crushers, which require fixed foundations. The mobility and quick setup of mobile units mean that they can follow the excavation or mining face, or move between multiple construction sites, providing on-demand crushing wherever needed.
Efficiency Comparisons: Crawler-Type vs. Wheeled Jaw Crushers
Both crawler-type (tracked) and wheeled mobile jaw crushers provide on-site crushing capabilities, but they differ in mobility, fuel use, terrain handling, and overall efficiency. Here’s a detailed comparison:
Mobility & Setup: Crawler-type mobile jaw crushers have excellent on-site mobility. They can inch forward or relocate on their tracks with ease, and be operational within minutes of arriving at a site. Operators can drive a tracked crusher directly to the work face without external assistance. In contrast, wheeled mobile jaw crushers must be towed or transported by a truck to the desired location. Positioning a wheeled crusher typically takes longer – the unit must be backed into place and sometimes supporting legs or jacks need deployment. Once in position, wheeled crushers might require auxiliary conveyors to connect with other equipment, whereas tracked units often have optimized layouts that minimize additional conveyors. Overall, for projects requiring frequent moves or quick setup (e.g. moving along a pipeline route or between short-term jobs), a crawler unit offers higher operational uptime due to its rapid redeployment.
Terrain Adaptability: Crawler units are designed for rugged terrain. The tracked undercarriage provides a low ground pressure and a strong grip, allowing the crusher to traverse soft ground, steep slopes (often up to ~30° incline), and uneven, muddy sites. This makes tracked jaw crushers ideal for mining sites, quarries, or hilly construction projects where terrain can be challenging. Wheeled mobile crushers, by comparison, perform best on relatively firm, level ground like roads or well-compacted soil. They are easier to move on highways and paved areas but can struggle or require assistance on muddy or uneven sites. If a project involves off-road mobility or working in areas without infrastructure, crawler crushers clearly have the advantage. Wheeled crushers may need access roads or flat pads prepared, which adds to site preparation time.
Fuel Consumption & Efficiency: Fuel usage can differ between tracked and wheeled units. Tracked mobile jaw crushers carry their engine and power system with them; when relocating on tracks, the diesel engine works to move a heavy machine, consuming significant fuel. Tracks themselves create more friction than wheels, which can lead to higher fuel consumption per hour of movement. However, during actual crushing operation, modern tracked crushers are designed to run efficiently — many use load-sensing hydraulics or variable speed engines to optimize fuel burn. Some models even allow switching to electrical power (via an external supply) once in place, effectively eliminating diesel usage during crushing if electricity is available. Wheeled mobile jaw crushers often have an advantage in pure fuel efficiency during operation: if they are electrically driven (for example, connected to a generator or grid power), they can have lower energy costs per ton of material crushed. Even wheeled units with onboard diesel generators tend to have efficient, fixed-RPM operation when crushing, since they don't need to power a crawler system continuously. Additionally, when moving between sites, a wheeled crusher transported on a truck doesn’t consume its own fuel for travel (the truck does that job). In summary, a wheeled plant can sometimes achieve a lower fuel cost per ton than a tracked plant, especially in long, continuous projects where the crusher stays in one place for a long time. Tracked crushers might burn more fuel while repositioning frequently, but they save time and labor by not requiring separate hauling equipment for short moves.
Productivity & Uptime: The productive output (throughput in tons per hour) of crawler vs. wheeled jaw crushers of similar size is usually comparable when they are actively crushing. Both types can house identical jaw crusher modules (for example, a 1000mm x 600mm jaw on tracks or on wheels will have similar theoretical capacity). However, some subtle differences affect overall productivity:
- Tracked crushers minimize idle time between shifts in location. They can be operational sooner after relocation, which is beneficial for projects that demand intermittent or distributed crushing. This means less downtime waiting for setup, boosting effective productivity over a project timeline.
- Wheeled crushers often come with larger feed hoppers or integrated surge bins (since they can afford a bit more weight and space on the trailer). A larger hopper can translate to more consistent feeding and slightly better throughput if loading equipment is slower. Also, maintenance access on wheeled units is generally easier (no track frames in the way), which can reduce service downtime for tasks like replacing wear parts or doing repairs.
- On the other hand, tracked systems are highly integrated; the crushing and moving functions work in tandem. In a multi-stage operation, a tracked jaw crusher can directly feed a secondary crusher or screen without complex arrangements, often via short conveyors, ensuring smooth material flow. This integration can enhance throughput by reducing spillage or intermediate stockpiling. Wheeled setups might require additional transfer conveyors between a mobile jaw and secondary units, and repositioning those can take extra time.
One noted difference is in mechanical uptime: tracked machines typically have more components under continuous stress (like the track drive system). Industry experience suggests that tracked systems may have slightly lower overall uptime (due to maintenance needs on the tracks and hydraulics) compared to simpler wheeled systems For instance, maintaining the track bearings and motors is an added task that wheeled units don’t have. That said, modern track-mounted crushers are engineered for reliability, and routine maintenance keeps downtime minimal.
Technical Specifications & Comparison Table
Mobile jaw crushers are produced in various sizes and configurations to meet different project requirements. Key specifications include the size of the jaw crusher (feed opening dimensions), engine or motor power, processing capacity, and overall weight of the machine. The following table compares specifications for a few representative mobile jaw crusher models (both crawler and wheeled types):
Model | Chassis Type | Feed Opening (mm) | Engine Power | Throughput Capacity | Total Weight |
---|---|---|---|---|---|
Crawler Jaw Crusher – Large (e.g. 1060 model) | Crawler (Tracked) | 700 × 1060 | ~150 kW Diesel-Hydraulic (110 kW crusher motor) | 150 – 400 tph (tons/hour) | ~41 t |
Crawler Jaw Crusher – Compact (e.g. 650D “Mini”) | Crawler (Tracked) | 500 × 700 | ~75 kW Diesel-Hydraulic | 50 – 130 tph | ~30 t |
Wheeled Jaw Crusher – Large | Wheeled (Portable) | 1050 × 750 | ~150 kW Diesel-Electric | 120 – 300 tph | ~35 t (excluding truck) |
Wheeled Jaw Crusher – Compact | Wheeled (Trailer) | 600 × 400 | ~90 kW Diesel or Electric Motor | 40 – 100 tph | ~20 t (excluding truck) |
Table: Sample specifications for different mobile jaw crusher models. The crawler large model (for example, similar to a 700×1060mm jaw unit) features a bigger jaw capable of high throughput (150-400 tons per hour) and is powered by a robust diesel engine driving a hydraulic system. Its total weight (around 40-45 tonnes) reflects the heavy-duty tracks and frame needed for rough terrain. The compact crawler model (often called a “mini” mobile jaw crusher) has a smaller 500×700mm jaw, lower power, and a lighter weight around 30 tonnes, making it easier to transport while still offering ~50-130 tph output for small to medium jobs.
For wheeled models, a large unit might use a similar jaw size (around 1050×750mm) and comparable crusher power. The listed weight for wheeled crushers often excludes the towing vehicle; unlike crawlers, wheeled crushers may not carry their own locomotion weight. A compact wheeled jaw crusher with a 600×400mm feed opening can be considerably lighter (around 20 tonnes) and typically needs to be pulled by a truck, but it provides an economical solution for lower volume crushing.
Note: Specifications can vary by manufacturer. Engine power might be listed as the power of the entire system or just the crusher motor. In the table, we’ve indicated typical ranges. Many modern mobile jaw crushers also offer optional equipment such as pre-screening grizzlies (to filter fines), over-band magnetic separators (to remove metal like rebar), and dust suppression systems. These options can slightly affect the weight and capacity of the machine. Always refer to manufacturer datasheets for precise numbers when comparing models.
Cost Analysis
Investing in a mobile jaw crusher involves evaluating both initial costs and long-term expenses. Below is a breakdown of cost factors to consider:
- Initial Purchase Cost: Crawler-type mobile jaw crushers generally have a higher capital cost than wheeled ones of similar capacity. The advanced tracked undercarriage, integrated power units, and reinforced frames add to the manufacturing cost. For example, a large tracked mobile jaw crusher can cost significantly more upfront (sometimes 20-30% higher or more) than a comparable wheeled portable unit. However, that higher price buys greater mobility and possibly eliminates the need for additional equipment (like loaders or haul trucks in some use-cases). Wheeled jaw crushers are often more budget-friendly initially; they are essentially crushers on a simpler trailer frame, without the expensive crawler system. For companies with tight budgets or those deciding between a stationary plant plus trucks vs. a mobile unit, wheeled crushers can be an attractive entry point into mobile crushing.
- Transportation and Deployment Costs: While initial price of machinery is one aspect, consider the cost to move and set up the crusher. A tracked mobile jaw crusher can self-deploy on site, saving on crane or transporter fees at the work site. You drive it off the trailer and it’s ready to go. A wheeled crusher often requires a compatible truck to tow it and possibly a crane or additional labor to position it, especially if it’s a larger trailer that needs assembly (like attaching conveyors). If your operations involve frequent site changes, the costs of transporting a wheeled unit (permits for road travel, escort vehicles for oversized loads, etc.) can add up. Tracked units, although heavier to transport, might reduce local movement costs because they can reposition themselves once dropped off.
- Operational Expenses (Fuel & Energy): Fuel consumption is a major operating cost for mobile crushers. Tracked jaw crushers running on diesel will incur fuel costs both for crushing and for any repositioning on site. As mentioned in the efficiency section, tracked machines may burn a bit more fuel per ton due to the added load of hydraulic systems. If diesel is the only power source, high utilization of a large crawler jaw crusher can lead to substantial fuel bills (hundreds of liters per day in continuous use). Many modern designs mitigate this with efficient engines, load-sensing systems, and idle control. Some even allow plugging into mains electricity or using hybrid drives – when available, using electric power can drastically cut fuel costs and is cheaper per kWh than diesel. Wheeled mobile jaw crushers often run the crusher via electric motors (from a genset or external power). This can yield a lower energy cost per ton, especially if grid power is accessible or if the diesel generator is optimized for constant load. In summary, if running on diesel only: expect roughly similar fuel costs for both types at equivalent workloads, with possibly a slight edge to wheeled units in efficiency. Over a long period, even a 5-10% difference in fuel consumption can translate to considerable savings.
- Maintenance & Wear Costs: All crushing equipment requires maintenance, but the types of maintenance differ for tracked vs. wheeled units. Tracked units have additional components like track chains, pads, rollers, and hydraulic motors – these wear over time. Replacing or servicing track parts (especially on large machines) is costly; for instance, a set of tracks can represent a significant expense every few thousand hours of use. Regular upkeep like greasing the tracks, tensioning them, and keeping the undercarriage clean is essential to avoid premature wear. This maintenance is an added cost (both parts and labor) that wheeled units largely avoid (wheeled units may need tire replacements, but tires generally last long in crusher applications because they aren’t continuously driven; plus, tires cost less than heavy steel tracks). On the other hand, wheeled crushers might have more maintenance on axles, suspension, and one often overlooked aspect: since they rely on being moved by trucks, the coupling systems (kingpin, brakes, lights, etc.) must be maintained to be road-legal. Both types share maintenance costs for the engine (oil changes, filters), the jaw crusher (jaw plate wear, toggle plate, bearings), and conveyors (belt replacement, roller maintenance).
- Wear Parts and Output Costs: The cost per ton of crushed material also depends on crusher wear parts and efficiency. A mobile jaw crusher’s jaw plates typically wear with use – harder, abrasive rock will wear them faster. These costs are comparable whether the unit is tracked or wheeled, as they use similar jaw mechanisms. However, running a jaw crusher efficiently (consistent feed, avoiding uncrushable material) will reduce wear costs. If a mobile unit (tracked or wheeled) is used correctly (with perhaps a pre-screen to remove fines or an iron remover magnet to catch metal), it can achieve a low cost per ton by extending the life of wear parts. It’s important to note that jaw plates and bearings are expensive, so ensuring proper maintenance intervals is key to cost control. Some users find that the overall cost per ton for mobile crushers can be lower than a stationary setup when factoring in the savings from on-site processing (less trucking of raw material and fill, for example) – even if fuel and maintenance are higher, you might eliminate external costs like dump fees or purchase of base material.
- Longevity and Resale: Another aspect of cost is the lifespan and resale value of the equipment. Tracked machines, being more complex, might have a shorter economic life before major refurbishment is needed (e.g., track motors or swing bearings might need overhaul after a number of years). Wheeled machines, with simpler frames, could have a longer service life or second-hand market in regions where towing is easier. However, high-quality tracked machines from reputable manufacturers often hold their value well if properly maintained, because the demand for efficient, self-contained crushers is high. When calculating total cost of ownership, consider how long you plan to use the crusher and its likely resale or trade-in value down the line.
In summary, crawler mobile jaw crushers demand a higher initial investment and slightly higher upkeep (fuel and maintenance), but they deliver unique savings in deployment and can tackle projects in ways wheeled crushers cannot. Wheeled mobile jaw crushers are typically cheaper to buy and run in stable environments, but you may incur extra costs in moving them and setting them up for each new project. For many contractors, the decision comes down to the scale and nature of work: large-scale, constantly moving operations favor the agility of tracked crushers, while projects with a fixed site or limited moves may find wheeled units more cost-effective. In either case, evaluating the total cost per ton of material produced – including machine costs, labor, fuel, and transport – will give the clearest picture of economic performance.
Practical Applications of Mobile Jaw Crushers
One reason mobile jaw crushers are so important today is their wide range of applications across different industries. They excel in situations where crushing needs to happen close to the material source or where a portable solution is required. Below are several practical use cases and examples:
- Construction and Demolition Recycling: Mobile jaw crushers are frequently used at construction sites to recycle concrete, asphalt, and other demolition debris. For example, when an old building or pavement is demolished, a mobile jaw crusher can be brought in to crush the concrete on-site. The crusher breaks down large chunks of material (like concrete slabs, bricks, and asphalt) into smaller aggregates that can be reused as fill or base material for new construction. This not only reduces waste hauling costs but also provides recycled aggregate for immediate use. Case in point: On an urban redevelopment project, a contractor might deploy a mobile jaw crusher to process the torn-up concrete foundations directly into 3” minus material for backfilling, eliminating the need to truck in quarry stone. The mobility of the crusher allows it to be positioned in a convenient spot (even in tight city environments) and moved as sections of the site are cleared. Additionally, any rebar or steel in the concrete can be removed using the crusher’s built-in magnets, simplifying disposal and recycling of metals.
- Road Building and Infrastructure Projects: In road construction, mobile crushers are used to prepare aggregate base and handle excavated rock or aggregate on the project site. For instance, during highway expansion or new road construction through rocky terrain, mobile jaw crushers can be set up to crush blasted rock into base layers right where it’s excavated. This is highly efficient – instead of transporting raw stone out and bringing crushed stone in, the same material is processed in place. Mobile jaw crushers on tracks are especially useful for road projects that progress over distance: the crusher can move forward along with the project, or be relocated to different sections of a long highway job as needed. One example is in rural road development, where a mobile jaw crusher might follow an earthmoving fleet, crushing local rock (from cuts or nearby quarries) into gravel that will form the roadbed. The quick setup means minimal interruption to the construction timeline. Moreover, for infrastructure projects like bridges or tunnels, a mobile jaw crusher can process the rock excavated from foundations or tunnel boring, turning potential waste into valuable fill or aggregate.
- Mining and Quarrying Operations: In mining, especially open-pit mining, mobile jaw crushers are used as primary crushing stations. They can be positioned at the mine face to crush large chunks of ore or rock right after blasting. This is particularly useful in mines where the digging face continuously moves as mining progresses. A classic scenario is an open-pit mine where a mobile jaw crusher is stationed at the edge of the pit and receives rock from haul trucks or excavators. By crushing the rock on-site, the volume of material needing to be transported out of the pit is greatly reduced (only the crushed, smaller ore goes to the next processing stage or to the plant). This can lead to significant savings in truck fuel and turnaround time. For example, in a coal mine, a mobile jaw crusher might be used to reduce raw coal to a manageable size before it’s transported by conveyor or truck to the preparation plant. In hard rock metal mining, tracked jaw crushers might handle the primary breakage of ore such as gold or copper-bearing rocks, improving logistics by moving with the mining front. Quarries (which are essentially open-pit mines for construction aggregates) also benefit: a mobile jaw crusher can replace a stationary primary crusher in a quarry that has long, extended reserves, saving the cost of building permanent crusher foundations multiple times as the quarry expands. Some aggregate producers use mobile jaw crushers to supplement stationary operations – for instance, to crush excess stockpiled rock or to operate in satellite quarry areas that are far from the main stationary plant.
- Remote or Temporary Projects: Mobile jaw crushers prove their value in remote locations or temporary projects where installing a stationary crusher isn’t feasible. Examples include military engineering projects, remote construction camps, or exploratory mining sites. If a project is short-term (say a dam cleanup, a temporary industrial demolition, or an emergency landslide clearing), a mobile jaw crusher can be rented or brought in for the duration of the work and removed afterward, with minimal site impact. Consider disaster relief scenarios: after a major earthquake, rubble from collapsed buildings can be crushed on-site using mobile crushers, facilitating quicker cleanup and providing materials for rebuilding roads or temporary shelters. The compact mobile jaw crusher (mini) units are particularly suited for such tasks, as they can be transported on small trailers and deployed in tight areas while still offering substantial crushing capability for their size.
Each of these applications highlights the convenience and efficiency mobile jaw crushers bring. By having a crusher at the point of material generation, companies save on transportation, reduce project timelines, and often lower overall costs. Moreover, the ability to produce reusable aggregate on-site aligns with sustainable practices – for instance, recycling concrete and reusing it reduces the demand on natural aggregates and cuts down waste in landfills. The case studies and examples in construction, road building, mining, and emergency projects all demonstrate that mobile jaw crushers are not just machines, but strategic assets that adapt to project needs and drive productivity in ways traditional setups cannot.
Environmental Impact & Fuel Efficiency
Modern mobile jaw crushers are engineered to minimize environmental impact and maximize fuel efficiency, addressing increasing regulatory and societal demands for cleaner operation. There are several facets to consider:
Emissions Control: Diesel engines are the workhorse of mobile crushers, and over the years, engine manufacturers have significantly reduced exhaust emissions. Most contemporary mobile jaw crushers come equipped with engines compliant with strict emission standards (such as EU Stage III/IV or US EPA Tier 3/Tier 4 Final). These engines include advanced exhaust after-treatment systems like diesel particulate filters (DPF) and selective catalytic reduction (SCR) to cut down on soot and NOx emissions. For example, a large crawler jaw crusher might use a Tier 4 Final engine that dramatically lowers emissions of nitrogen oxides and particulates compared to older models. This means that on-site crushing generates less air pollution, benefitting both the environment and the health of workers nearby. In regions like Europe and North America, using compliant low-emission mobile crushers is often not just a choice but a requirement for legal operation on job sites. Even in developing regions, the trend is toward cleaner engines (e.g., China’s National III/IV standards mentioned for some equipment correspond to similar progressive emission requirements).
Fuel Efficiency Technologies: Fuel efficiency goes hand in hand with emissions – burning less fuel not only saves cost but also reduces CO₂ output. Mobile jaw crusher manufacturers have introduced a range of technologies to improve fuel efficiency:
- Load-Sensing Hydraulics: In hydraulic-driven crushers, the system can adjust pump output based on load. When the crusher isn’t under full load or when idling, the engine throttles down to consume less fuel. This prevents the engine from running at high RPM unnecessarily.
- Engine Auto-Idle and Shutdown: Many modern units have an automatic idle feature – if the crusher is not crushing material for a certain period (for instance, waiting for the next load), the engine RPM drops to idle, or the system may even shut the engine off after extended inactivity. This conserves fuel during delays.
- Variable Speed Drives: In diesel-electric crushers, the generator and electric motors can be fine-tuned for optimal performance. Electric drives often have high efficiency across varying loads, meaning they use power more effectively than purely hydraulic systems at partial loads.
- Hybrid Power and Electric Operation: A significant advancement in reducing fuel consumption is the introduction of hybrid and plug-in electric capabilities. Some tracked mobile jaw crushers offer a dual power option – they can run on the diesel engine or be connected to an external electrical supply. On a site with grid power or a portable genset, the crusher’s drive motors can be powered electrically, cutting out diesel usage entirely while in electric mode. This drastically reduces fuel consumption (essentially to zero when plugged in) and also lowers noise levels and emissions on site. Even when running on diesel, the ability to switch to electric when available adds operational flexibility and sustainability. For example, a contractor might use diesel power in remote locations, but once the project moves closer to a site with electricity (or during daytime when solar power is available from a site grid), they plug the crusher in.
- Improved Engine Designs: The engines themselves are more efficient than older generations. High-pressure common rail fuel injection, turbocharging, intercooling, and electronic control units (ECUs) allow these engines to get more power out of each drop of fuel. Some quotes from users note that a modern mobile jaw crusher “can run all day on a surprisingly small amount of fuel” compared to machines a decade old, thanks to these improvements
Noise and Dust Suppression: Environmental impact isn’t only about emissions and fuel. Mobile jaw crushers, by nature of breaking rock, can generate significant noise and dust. To mitigate noise, manufacturers incorporate sound-damped engine housings, improved mufflers, and even noise blankets around the crusher in some cases. Tracking systems are also getting quieter – rubber pads on tracks (when crossing concrete/asphalt) and smoother hydraulics reduce the clanking and whining sounds. Dust is addressed by integrated water spray systems at the jaw intake and conveyor discharge. These sprayers moisten the material, preventing dust clouds. Controlling dust is not only environmentally responsible (reducing particulate matter in air) but also improves the health and safety conditions for workers on site and neighbors in urban job locations. Some mobile jaw crushers have optional dust encapsulation covers or attachable enclosures around conveyors to further contain dust spread.
Eco-Friendly Materials and End-of-Life: While not immediately obvious during operation, there’s a sustainability aspect in the construction of the machines themselves. Reputable manufacturers use environmentally friendly manufacturing processes and materials. Additionally, by enabling recycling of materials (as discussed in applications), mobile jaw crushers contribute to a circular economy in construction. Every ton of concrete or asphalt recycled on-site is a ton of natural aggregate saved and one less ton of waste in a landfill. This reduces the overall environmental footprint of construction projects.
Finally, consider the carbon footprint reduction. By using a mobile crusher at the site, companies drastically reduce the trucking required. Fewer dump trucks hauling material back and forth means lower CO₂ emissions from those vehicles. One could calculate that a project which crushes on-site might eliminate dozens of truck trips, equating to significant fuel and emissions savings over the project duration. In this way, mobile jaw crushers indirectly prevent pollution by replacing what would have been done by multiple machines (haul trucks, stationary crusher run by grid power often from fossil fuels, etc.) with one efficient, optimized unit.
In summary, modern mobile jaw crushers are far “greener” than earlier generations. Through advanced engines, hybrid technology, better fuel economy, and added features for dust and noise control, they reduce their environmental impact while still delivering the required productivity. This alignment with environmental goals not only helps companies meet regulations and corporate sustainability targets but also often goes hand-in-hand with cost savings (fuel saved is money saved). The industry trend is clear: mobile crushing equipment is becoming more energy-efficient and eco-friendly, ensuring that high-performance crushing can coexist with environmental responsibility.
Integration with Other Crushing & Screening Equipment
Mobile jaw crushers typically serve as the primary crushing stage in a multi-stage processing operation. For a complete aggregate production or recycling solution, they are usually integrated with other mobile crushing and screening units. This modular approach allows operators to create a streamlined processing train that can handle raw material from start to finish. Here’s how mobile jaw crushers complement other equipment:
- Primary Stage – Mobile Jaw Crusher: The process often begins with a mobile jaw crusher handling the largest pieces of rock or debris. The jaw crusher’s job is to take input material (which could be big chunks of blasted rock or chunks of concrete) and reduce it to a size that downstream machines can handle. For example, a jaw might crush 600mm boulders down to 150mm. This primary crushed output is usually a mix of sizes that requires further reduction or classification. The mobile jaw’s ability to move to the source of material means it can continuously feed the next stages with freshly crushed material, minimizing material handling.

- Secondary Stage – Mobile Cone Crusher or Impact Crusher: After the jaw crusher, the material often needs to be made smaller or shaped for specific uses. This is where secondary crushers come in. A mobile cone crusher is typically used for hard, abrasive stones where you need to produce cubical aggregates (such as for concrete or asphalt). The cone crusher takes the 100-200mm stone from the jaw and crushes it down to, say, 20-50mm or smaller, depending on the desired output. Alternatively, a mobile impact crusher may be used as the secondary unit, especially in recycling or softer stone applications. Impact crushers excel at shaping material and can handle things like concrete with rebar (the impactor can break the binding and release the steel, which can then be removed by magnets). They produce good-quality aggregate for road base or fill. In a recycling setup, a jaw crusher might crush concrete to intermediate size, then an impact crusher can further reduce and also improve the shape of the final product (e.g., turning it into fine usable aggregate). Integration is key: the mobile jaw feeds the mobile cone or impact through a conveyor. Some setups use an intermediate conveyor with a screen (often called a scalping screen) between the jaw and secondary crusher to remove fines or small material that doesn’t need further crushing. This improves the efficiency of the secondary crusher (it only processes the pieces that truly need size reduction).
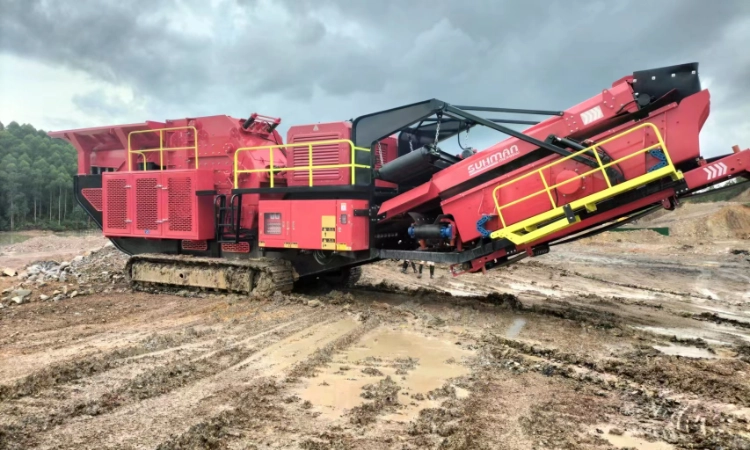
- Tertiary Stage (if needed) & Screening – Mobile Screening Plant: Once the material has been through primary and secondary crushing, you often have a range of particle sizes. A mobile screening plant is then used to sort the crushed material into different size fractions. For instance, after a jaw + cone crushing sequence, you might have a pile of 0-20mm, 20-50mm, and oversize >50mm. The screening plant will have one or multiple decks of screens that vibrate to separate the sizes. The oversize can be sent back (via return conveyor) to the crusher (either the secondary cone or back to the jaw) for further crushing – this loop is referred to as a closed-circuit operation. Meanwhile, the desired product sizes (e.g., 0-10mm sand, 10-20mm gravel, 20-40mm stone) are stockpiled by the screener’s conveyors or collected for use. Mobile screening units are highly efficient and can be paired with crushers to ensure that the final output meets specifications. For example, in road construction, you might need a particular gradation of aggregate – the jaw + secondary crusher provide reduction, and the screening plant ensures only the right sizes are delivered.
Beyond these primary roles, integration can involve more specialized equipment:
- Some mobile jaw crushers come with an attached vibrating screen unit under the crusher (known as a jaw crusher with integrated screen). This setup can produce a sorted output directly from the jaw for specific applications (like producing a uniform fill material and removing fines simultaneously).
- Stackers and Conveyors: While each mobile unit has its own conveyors, large operations use additional mobile stacking conveyors to pile up final products or to transfer material over longer distances (for example, from the screening plant to a huge stockpile). These stackers are mobile and keep the operation continuous without needing loaders to move material as much.
- Coordinated Control Systems: In an integrated mobile spread, the jaw crusher, cone/impact crusher, and screening plant can be electronically linked. This means the system can automatically adjust feeder speeds and conveyor speeds to balance the material flow. For instance, if the cone crusher downstream is getting overloaded, it can signal the jaw crusher’s feeder to slow down a bit, preventing a pile-up and optimizing throughput. Such smart integration improves efficiency and reduces the chance of stoppages.
Example of a Full Integration: Imagine a large demolition concrete recycling project. The integration might work as follows: A mobile jaw crusher takes all the demolished concrete (with rebar) and crushes it to ~150mm. A cross-belt magnet on the jaw’s discharge conveyor pulls out most of the rebar. The material then goes to a mobile impact crusher as secondary crushing, which further reduces it to <40mm and also liberates any remaining embedded metals. After the impactor, the material is conveyed to a mobile screening plant which separates it into 0-10mm sand (to be reused as fill or sand substitute), 10-40mm aggregate (to be used as recycled concrete aggregate for new concrete or road base), and >40mm chunks (which get sent back to the impact crusher for another pass). Throughout this process, the three machines are located close together, minimizing conveyor lengths and transfer points. The outcome is a seamless production line that turns raw waste into sorted, valuable materials in one continuous operation – all achieved with mobile equipment that can be packed up and moved once the job is done.
Mobile Jaw + Cone combinations are common in hard rock quarries (jaw does primary, cone does secondary), while Jaw + Impact is common in recycling (jaw primary, impact for shaping) or softer stone. In some cases, three-stage crushing is used (Jaw > Cone > Impact or Jaw > Impact > Impact for very high reduction), but this is less common with mobiles due to transport considerations – however, some large operations do train multiple crushers in a line.
Integration also allows for scalability. Contractors can add or remove units based on project demands. Need more production? Add another cone crusher or a second screening plant. Job winding down? Remove the secondary stage and just run a jaw + screen for simple production. The modular nature of mobile crushing trains gives operators tremendous flexibility.
In essence, a mobile jaw crusher rarely works alone in high-volume aggregate production. It is the first stage of a coordinated process. When properly integrated with cone/impact crushers and screens, it forms a complete mobile crushing and screening circuit capable of transforming raw feed into various finished products efficiently. This turnkey solution is what enables mobile equipment to rival traditional fixed plants in output while retaining superior mobility.
Choosing the Right Mobile Jaw Crusher
Selecting the most suitable mobile jaw crusher for your needs involves careful consideration of multiple factors. The “right” choice depends on the type of project, material characteristics, production requirements, and budget constraints. Here are key factors and guidelines to help in the decision-making process:
- Material Type and Hardness: Start by evaluating the material you plan to crush. Is it hard rock (like granite or basalt), medium hardness (limestone or concrete), or softer material? Different jaw crusher models are built to handle varying hardness levels. For hard and abrasive rocks, you’ll need a robust crusher with high wear resistance (strong jaw plates, possibly a smaller feed opening to increase crushing force). For softer materials, you might prioritize a larger feed opening and higher throughput instead of sheer crushing power. Additionally, if you expect a lot of rebar or steel in the material (such as in reinforced concrete demolition), ensure the jaw crusher has features like a hydraulic release or an iron separator to deal with uncrushable pieces without damage.
- Feed Size and Feed Opening: The size of the input material dictates the feed opening you need. A general rule is that the feed opening of the jaw crusher should be larger than the largest dimension of your raw material by a comfortable margin. For example, if your blasted rock or raw chunks are about 500 mm at their biggest, you’d want a jaw crusher with at least a 600 x 400 mm feed opening (so it can easily accept 500 mm rocks without constant jams). If you choose a machine with too small a feed opening, you’ll spend extra time pre-breaking material or risk clogging the crusher. Conversely, a very large feed opening on a small project might be overkill – larger crushers have bigger appetites not just for rock, but also for fuel and space. So, match the jaw size to your material size. Keep in mind that mobile jaw models are often denoted by the feed opening dimensions (e.g., “1060” jaw might refer to approx 1000 x 600 mm opening).
- Output Size and Production Capacity: Consider the required output sizes (product size) and capacity (tph). If you need to produce a specific grade of aggregate, ensure the jaw crusher can be adjusted to that output size or that you have secondary crushers to achieve the final size. Jaw crushers produce relatively coarse output (often 100mm+ unless a tight closed side setting is used). If you need very small output (say <40mm) and only a jaw crusher in your setup, you’ll want a jaw capable of a tight setting (and perhaps a smaller model, because extremely large jaws typically can’t close down to very small gaps). Regarding capacity, assess how many tons per hour you need to process. Manufacturers rate mobile jaw crushers at continuous crushing capacity under ideal conditions. It’s wise to choose a crusher that can exceed your required capacity by some margin, ensuring it can handle peak loads or slightly harder material without slowing down. For instance, if you need 100 tph, consider a machine rated for 120-150 tph to have a buffer. Also, consider the efficiency of the whole train – if the jaw is feeding other equipment, balance capacities so one machine isn’t choking the rest.
- Mobility Needs (Tracked vs. Wheeled): Decide if you need a crawler-type or wheeled mobile jaw crusher (as discussed earlier). This heavily depends on the project terrain and how frequently you need to move the crusher. Ask yourself:
- Will the crusher need to move frequently within the job site (daily or weekly)? If yes, a tracked unit will save a lot of time and effort.
- Are the job sites far apart geographically, requiring road transport often? If you’ll be moving the crusher from site to site via roads every month or so, a wheeled unit might be easier (no low-bed trailer needed in some cases, just tow it).
- Is the ground at job sites prepared or rough? For unprepared, rough ground like a mine, tracked is safer. For well-prepared construction sites or recycling yards, wheels could suffice.
- Do you have the transport equipment for each type? Owning a lowboy trailer and heavy tractor might be necessary for large tracked crushers anyway, but smaller wheeled crushers could be towed by a standard truck unit.
- Space and Access Constraints: Evaluate the physical footprint of the crusher and the space available on site. Urban and indoor demolition jobs, for instance, might require a smaller, more compact crusher that can navigate narrow streets or even fit indoors. In such cases, a mini mobile jaw crusher (compact design) is advantageous. These smaller units (often with around 500 mm or less feed openings and lower profiles) can operate in courtyards or inside large buildings being demolished, where bigger crushers can’t fit. Conversely, if space is not an issue (e.g., open pit mine), you can afford the luxury of a larger machine with bigger output, even if it’s bulkier. Check also the setup dimensions – including when conveyors are deployed. Ensure there’s room for loading equipment to feed the crusher and room to stockpile product or to place a secondary crusher/screener if part of your plan.
- Budget and Cost of Ownership: Initial budget will dictate the range of models you can consider. However, think beyond just purchase price:
- If a certain model is more expensive but can handle the job with one unit instead of you using multiple smaller units, it might save money in the long run.
- Consider fuel efficiency differences – a cheaper machine that guzzles fuel will cost more over time than a slightly pricier one that’s efficient.
- Look at warranty and support: some manufacturers offer comprehensive support packages, which can be worth it in reducing downtime.
- If buying new is too costly, some opt for used mobile crushers – but ensure you inspect wear (especially jaw condition, engine hours, track condition) and consider that older models might not meet current emissions standards if that’s a concern for your projects.
- Manufacturer Support and Parts Availability: Mobile jaw crushers are complex, so strong after-sales support is crucial. Research the manufacturer or brand – do they have local service centers or technicians? How easy is it to get spare parts like jaw plates, filters, belts, or hydraulic components? Choosing a popular model from a reputable manufacturer can mean parts are readily available, even overnight in emergencies. If you select an uncommon brand or a very new model, parts might have to be imported, which can lead to longer downtimes when maintenance is needed. Also consider the simplicity of maintenance – some designs allow easier access to the jaw chamber or engine, which can save hours of labor during routine service.
- Special Features and Customization: Think about any special needs:
- Do you need a particular feature like an integrated prescreen (to remove fines), which some jaw models have to boost efficiency?
- Is an automated control system important for you (for example, to remotely monitor performance or integrate with other crushers in train)? Some modern crushers have telematics and remote controls.
- If working in urban areas, should you opt for additional noise suppression kits or dust control on the unit?
- If you foresee using electric power often, a model with a dual power (hybrid) option would be wise.
- For very abrasive rock, sometimes jaw crushers come with optional harder jaw plate alloys – if offered, it might be worth the investment to extend the time between jaw plate changes.
- Examples – Matching Crusher to Use Case: To illustrate selection:
- Small-scale building demolition & recycling: A city contractor might choose a compact tracked mobile jaw crusher (say with ~30 t weight) because it can be transported easily with a midsize trailer, fits on small sites, and is agile. The focus might be on having a machine that one operator can run with remote control to nibble away at a building and crush material on-site. Here, features like dust suppression and low noise are important due to urban setting.
- Large quarry primary crusher: An aggregate producer with a quarry might go for the largest tracked jaw crusher available that fits their blasting output. If the quarry consistently produces 0.5–1.0 meter boulders, a jaw with 1200mm+ opening is needed, likely a heavier tracked unit (~50-60 t class). They’d prioritize a machine known for reliability and high throughput, and they likely pair it with a cone crusher and screen. Mobility within the quarry is still important, so tracked is preferred; wheeled wouldn’t handle the pit well.
- Contract crushing on paved roads: A contractor who does crushing on contract for municipalities might lean toward a wheeled mobile jaw crusher. They often have to move on public roads, sometimes short distances between subdivisions. A wheeled unit can be towed without special transport permits (if it’s compact enough), saving logistic hassles. They’d also value quick setup outriggers and maybe an integrated generator that can power site lights or other tools.
- Mining operation in remote area: A mining company in a remote region might choose a tracked jaw with hybrid power. They can run it on diesel during initial site work, but once they establish a steady operation, they might hook it to their generator or grid line to save on diesel. They’ll look at fuel consumption rates, the capacity to handle hard ore, and robustness (since downtime in such locations is extremely costly).
Ultimately, choosing the right mobile jaw crusher is about balancing all these factors to your specific context. It may help to consult with the manufacturers or distributors – they often can perform simulations or use past data from similar projects to recommend a suitable model. Also, visiting an operation similar to yours to see a crusher in action can provide insight (for example, seeing how a compact crusher handles demolition waste can confirm if its capacity is truly enough for your volume).
Remember that the best crusher is one that efficiently and reliably meets your production goals with the lowest cost and hassle over its life. Taking the time to analyze your needs along the dimensions of material, mobility, capacity, and cost will pay off in selecting a machine that becomes a valuable asset rather than a bottleneck.
Conclusion
Mobile jaw crushers have revolutionized the way crushing is done in the field, offering a combination of power and portability that is essential for modern construction and mining operations. They bring the crushing plant directly to the job site, eliminating unnecessary material handling and streamlining the production of aggregates and recycled materials. As we’ve discussed, these machines are not one-size-fits-all; there are crawler and wheeled variants, from mini crushers to heavy-duty large models, each with their own strengths. The key is understanding your project’s demands and choosing equipment that aligns with those needs.
In today’s fast-paced and cost-conscious industry, the ability to rapidly deploy a crusher and start production can give companies a significant competitive edge. Whether it’s building new roads in remote areas, processing excavation rock on a construction site, or recycling tons of demolition concrete in an urban setting, mobile jaw crushers provide the flexibility and efficiency required. They have proven to lower overall project costs by reducing haulage, speeding up timelines, and enabling on-site reuse of materials. Furthermore, advances in technology have made these crushers more environmentally friendly – quieter, cleaner engines and even hybrid electric drives mean that productivity no longer comes at the expense of sustainability.
Mobile jaw crushers also seamlessly integrate with other equipment, forming complete mobile processing lines that can rival the output and quality of fixed installations. This integration capability underscores why they are central to mobile crushing and screening solutions around the world. Operators can scale their systems, add secondary/tertiary crushers, and fine-tune the output, all while keeping the entire operation mobile.
In essence, the mobile jaw crusher has become an indispensable tool for many sectors. Its importance will only grow as projects become more dynamic and as the emphasis on cost reduction and environmental responsibility increases. By allowing material processing to happen at the source, mobile jaw crushers help turn challenges (like remote locations, strict timelines, or waste materials) into opportunities (like on-site aggregate production and efficient resource use).
For companies in construction, infrastructure, or mining looking to modernize their operations, investing in a mobile jaw crusher (and the associated train of equipment) is often a wise decision. It ensures you’re not tied down to one location and can adapt to the needs of each project – large or small. The versatility, efficiency, and productivity of mobile jaw crushers underscore why they are considered essential equipment in the industry today. In a world where “time is money,” being able to crush materials whenever and wherever needed provides a clear advantage. Mobile jaw crushers epitomize this advantage, making them a cornerstone of modern aggregate production and recycling operations.