Mobile Crushing Differences Between Impact, Jaw, and Other Crushers
Release time: 2025-03-15
Introduction
Mobile crushing and screening equipment has revolutionized the way industries process materials on-site. Instead of hauling raw rock or demolition debris to a fixed plant, these portable machines enable “in-pit” crushing and sorting, drastically reducing transportation costs and setup times From quarries and mining operations to construction and demolition recycling, mobile crushers and screens play a vital role in turning large chunks of rock or concrete into usable aggregate. They offer flexibility (track-mounted or wheeled units can be relocated as the project evolves), rapid deployment, and high efficiency in various work conditions This comprehensive guide will explain the different types of mobile crushers – jaw crushers, impact crushers (horizontal and vertical shaft impactors), cone crushers, and hybrid models – along with their technical specifications. We’ll compare their working principles, ideal applications, and key performance parameters. For potential buyers, understanding these differences is crucial to select the right machine that balances capacity, product output, operational cost, and mobility for their specific needs.

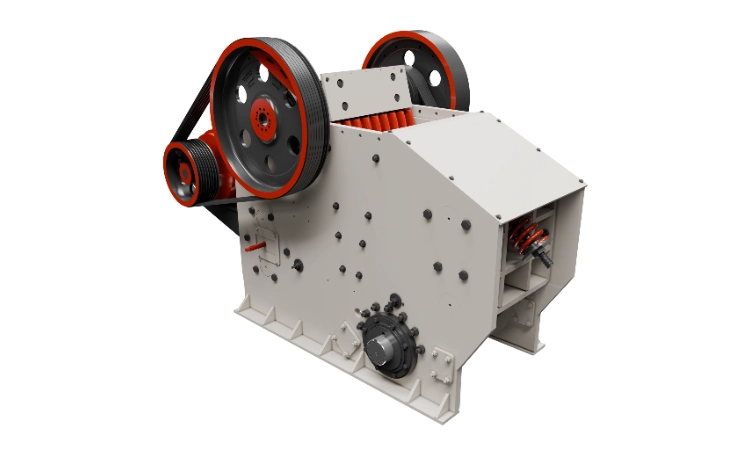
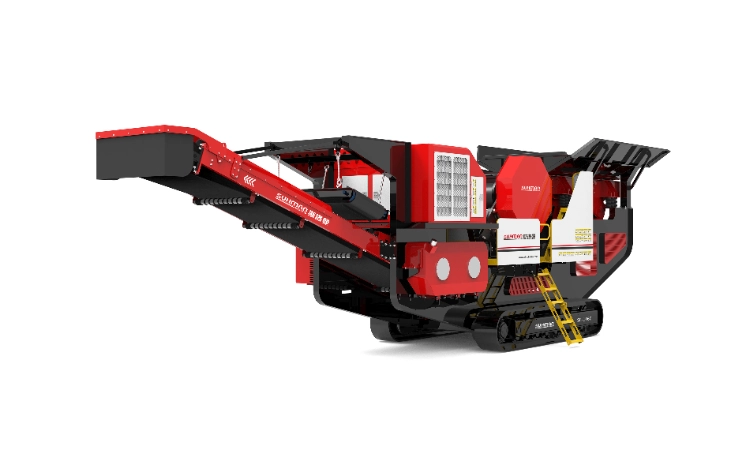
Crusher Types Explained
Mobile crushers can be categorized by the crushing mechanism they use. Each type has a unique working principle and is optimized for certain material types and end-product requirements. Below, we break down the main crusher types used in mobile units, including how they work, what materials they handle best, and their efficiency in different applications.
Jaw Crushers
Jaw crushers are compression crushers, widely preferred for coarse primary crushing of hard and large-sized materials They feature a V-shaped crushing chamber with two jaws – one fixed and one moving (the “swing” jaw) – that compress material until it breaks. The movable jaw, driven by an eccentric shaft, oscillates against the fixed jaw to crush the feed material Rock enters from the top opening and gradually gets crushed to smaller sizes as it travels downward, until the fragments are small enough to pass through the bottom gap (the closed-side setting) This mechanism delivers a typical reduction ratio of around 5:1 (large chunks reduced to roughly one-fifth of their original size in one pass)
Technical characteristics: Mobile jaw crushers can accept the largest feed size of any crusher type – often processing boulders up to 1000mm (1 meter) or more, depending on the model This makes them ideal for the first crushing stage (primary crushing) where raw material from the mine or excavation site is oversized. Jaw crushers are known for their ruggedness and reliability; they can handle very hard materials like granite or blasted rock with high compressive strength (up to ~300 MPa) They operate at relatively low speeds and require less horsepower compared to other crushers, making them energy-efficient for the work they do For instance, a jaw crusher’s flywheel and toggles store energy and release it with each crush, which means steady crushing power without constant high RPM demand. The throughput capacity of mobile jaw crushers is high – larger models can produce anywhere from ~100 up to 750+ tons per hour, and some heavy-duty versions even approach 1000+ TPH in ideal conditions However, because jaw crushers primarily produce a coarse output, they are often followed by secondary crushers to achieve finer gradations.
Ideal materials and applications: Jaw crushers excel at crushing hard, abrasive rocks (like granite, basalt) and large concrete pieces with rebar (the jaw’s opening can handle rebar to some extent, and any trapped steel can be removed later with magnets). They are a go-to for quarry primary crushing and for contractors processing excavation materials. Jaws also cope better with wet or sticky materials than some other crushers – for example, when dealing with moist cohesive soil or clay-laden gravel, a jaw is less likely to clog than a cone crusher The output from a jaw crusher is typically an intermediate size (often 4–6 inches or 100–150mm minus) which then might be fed into a cone or impact crusher for further reduction. In summary, use a jaw crusher when you need to accept very large feed, ensure reliability on hard material, and prefer a simpler, lower-maintenance crushing solution for the primary stage.
Efficiency and maintenance: Due to their straightforward design, jaw crushers tend to have lower wear-part costs and maintenance needs. The main wear items – the jaw plates – are thick, replaceable slabs that can endure a good amount of wear before needing change. Operators often flip or replace jaw plates periodically to maintain crushing efficiency. In general, a jaw crusher has fewer wear parts compared to an impact crusher and operates with less noise and dust generation They also don’t require daily sophisticated tuning – setting the output size (via adjusting the jaw gap or shims/hydraulic toggles) is relatively simple. However, buyers should consider that while jaws are robust, they do not typically produce the final finished product in one pass. If a very specific small size or cubical shape is required, a jaw crusher’s product will need additional processing by other crushers or a screening setup.
Impact Crushers (Horizontal Shaft and Vertical Shaft)
Impact crushers use high-speed impact force rather than compression to break rocks. They come in two main sub-types: Horizontal Shaft Impactors (HSI) and Vertical Shaft Impactors (VSI), each suited to different tasks. In both types, material is fed into a chamber where it encounters a rapidly spinning rotor or impeller, and breakage occurs by the sudden impact against crusher walls or impact bars. This yields a high reduction ratio and often a good shape on the final product, but with different operating nuances for HSI vs VSI.
Horizontal Shaft Impact (HSI) Crushers: An HSI has a horizontal rotor with fixed blow bars (metal hammers) that fling the incoming rock against breaker plates (also called aprons) lining the chamber. Think of it as throwing rock at high speed into a steel wall. HSIs usually feature a larger feed opening and can accept fairly chunky material (often up to 600–800mm feed, depending on the machine) This capability makes many HSIs suitable as primary crushers for softer rocks or as secondary crushers for medium-hard materials. Upon entry, rock is struck by the rotating blow bars and shattered; the fragments then hit the aprons and each other, further breaking down before exiting. The result is a high reduction ratio, often 8:1 or even 10:1, meaning an HSI can take, for example, 200mm feed and reduce it to ~20mm or less in one stage HSIs are known for producing a good proportion of cubical-shaped product (ideal for concrete and asphalt aggregates) and for their ability to handle contaminants (like a bit of rebar or wood in construction debris, which tends to pass through after breaking the concrete around it).
Ideal uses for HSI: They excel at crushing medium-hard to soft materials such as limestone, gypsum, asphalt, and concrete rubble . In quarry operations, an HSI is a great choice for limestone or medium-soft stone where a jaw might not be necessary. In recycling, HSIs are popular for concrete and asphalt recycling due to their high reduction and shaping ability. HSIs generally have high throughput capacities (several hundred TPH, depending on rotor size and power) and can be more forgiving with feed that has some fines or smaller material mixed in.
Vertical Shaft Impact (VSI) Crushers: VSIs employ a different approach – often described as “rock on rock” crushing. A VSI’s rotor is oriented vertically, spinning at high RPM, and it may either hurl material against rock lining inside the crusher or against static anvils (metal plates). Many VSIs use the rock-on-rock technique: the rotor throws material upward and outward, where it collides with material that is being hurled from other parts of the rotor, causing the pieces to break by impact and also by inter-particle collision. This mechanism is highly effective for shaping the final aggregate and producing sand. VSIs typically handle smaller feed sizes (often under 100mm, and in practice often <50mm) and are thus used in secondary or tertiary stages They may follow an HSI or a cone crusher once the material is already reduced and need further shaping or fine reduction. The hallmark of a VSI is the consistent, cubical product it creates, with excellent fine aggregates for asphalt, concrete sand, or base material . A VSI can turn a relatively flaky output from a cone crusher into a well-shaped final product with lots of fractured faces (good for binding in concrete or asphalt).
Ideal uses for VSI: These are often found in manufactured sand production, road base aggregate production, or any application where particle shape is critical. Many modern asphalt plants prefer material from a VSI for its cubical shape and the fines content that help with compaction. VSIs are also used in mineral processing for specific ores (like a shaping crusher in iron ore or to make fine aggregate in aggregate plants).
Efficiency and considerations (Impact Crushers): Impact crushers offer the advantage of high reduction efficiency in a single stage and typically yield more fines (powdery material) and a higher percentage of finished product passing desired sizes, compared to compression crushers This can be a pro or con: if you need fines (e.g., manufacturing sand), an impactor helps; if fines are waste in your process, a compression crusher might be better. Energy-wise, impacts do require higher horsepower to maintain the rotor speed especially when crushing hard material – effectively, they convert a lot of energy into the kinetic force for breaking rock and also into noise and heat. In fact, impact crushers tend to be louder and dustier than cones or jaws during operation Maintenance is a critical factor: the wear parts (blow bars on HSI, or rotor tips/anvils on VSI) wear down relatively faster. In abrasive stone (like granite), wear costs for an impactor can be considerably higher than for a cone crusher. However, the trade-off is the better product shape and simpler operation (no closed-side setting to adjust as frequently, no heavy flywheels or toggles). Modern impactors often have quick-change designs for blow bars and adjustable aprons to control output size, but a buyer should expect to replace wear parts more frequently than they would on a jaw or cone
To summarize, choose an HSI impact crusher if you need a primary or secondary unit that can quickly reduce medium-soft materials with high reduction ratio, or a VSI if your priority is fine output and superior particle shape for sand or fines. Keep in mind the higher wear and maintenance needs – impacts reward you with versatile crushing and product quality, but at the cost of more frequent inspections and consumable replacements.
Cone Crushers
Cone crushers are another type of compression crusher, designed typically for secondary and tertiary crushing stages. A cone crusher consists of a cone-shaped mantle that gyrates within a stationary concave bowl. As it spins, the gap between the mantle and concave opens and closes repeatedly. Rocks are trapped and crushed in this space through a combination of squeezing and bending (shear) until they are small enough to drop out of the bottom. This continuous crushing process (often called “lamination crushing”) is very effective for reducing material size gradually and produces a relatively uniform output. Unlike the hard “slam” of an impact crusher, a cone crusher exerts a gentler crush over a longer time, which can result in less generation of fines and a very stable, high-capacity operation
Technical characteristics: Cone crushers generally have a smaller intake than jaw crushers – they typically accept feed in the 200mm–400mm range for secondary cones, up to around 500–600mm for bigger primary gyratory-style cones Thus, they often follow a jaw crusher to handle the smaller feed. Cones are known for high production capacity: for instance, some large mobile cone crushers can produce well over 500 TPH, and stationary high-end cone crushers can reach 2000+ TPH under perfect conditions They also operate with relatively low energy consumption per ton of output because the crushing process is distributed and continuous The grain output from a cone is usually well-graded (a good mix of sizes) and finer on average than what a similar stage impact crusher might produce However, one downside is that the shape of aggregate from a cone crusher can be more elongated (more “needle-like” pieces) compared to the cubical shape from an impact crusher For many applications (e.g., base material or concrete that will be further processed), this is not a big issue, but for top-layer asphalt or high-spec concrete, a later shaping stage (like a VSI) might be added to improve shape.
Ideal materials and applications: Cone crushers thrive on hard, abrasive rocks such as granite, basalt, gabbro, iron ore, and other materials that would cause excessive wear to an impact crusher They are workhorses in mining and quarrying – commonly used after a primary jaw or primary gyratory to crush down to sizes around 1 inch (25mm) or less for aggregate, or even finer for mineral processing. In aggregate production, a typical setup might be a jaw crusher as primary (taking 600mm+ blasted rock), and a cone crusher as secondary (taking in 150–200mm feed from the jaw and crushing it down to 40–60mm). A third-stage cone or VSI might then follow for further reduction. Cones are also used in tertiary roles to make smaller aggregate, where they can be set to very fine outputs (e.g., 10–20mm or even less). Because of their ability to handle high hardness and produce at a stable rate, they are often chosen for high-volume projects or continuous processes (like industrial mineral crushing).
Efficiency and maintenance: Modern cone crushers are engineered for heavy-duty output but also with maintenance convenience in mind. They have replaceable wear liners (mantle and bowl liner) which typically last longer than the wear parts on impact crushers The longer wear-part life means less frequent downtime for liner changes, which is advantageous in high-production environments Cones often come equipped with hydraulic adjustment and clamping systems that let operators change the closed-side setting (CSS) – and thus the output size – on the fly or clear a jam (e.g., if uncrushable material enters, many cones have hydraulic relief to let tramp metal pass without damaging the machine). Automation features are common: load sensors can adjust feed rates to keep the crusher choke-fed (which is important for optimal cone performance), and modern control systems can monitor wear, power draw, and even automate liner calibration. In terms of power, cones do require a significant drive motor (often in the 200–500 kW range for high-capacity units) to generate the crushing force, but they apply that force more steadily and efficiently than an impact crusher’s sudden blasts. Consequently, operational costs (fuel or electricity per ton) can be lower for cones in many applications Buyers should note that cones, while reliable, work best when the feed is consistent (homogeneous and within the size range). They may struggle or see reduced efficiency if fed with a lot of fines or variability in feed size, which is why cones are often paired with screens or feeder systems to pre-sort material. Maintenance for a cone crusher mainly involves monitoring liner wear, keeping the lubrication and hydraulic systems in good condition, and occasional manganese steel liner replacements. Overall, a cone crusher is a durable, lower-maintenance choice for producers who deal with hard stone and need a predictable, continuous output with relatively low wear costs over the long term
Hybrid Models (Diesel-Electric Mobile Crushers)
In addition to the classic types of crushers, many modern mobile crushing plants are available in “hybrid” configurations. A hybrid mobile crusher uses a combination of a diesel engine and electric motors to drive the crusher and associated equipment (feeders, conveyors, screens). In essence, the diesel engine acts as a generator (and can often be bypassed when external electric power is available), while electric motors actually power the crushing unit and other components. These hybrid systems bring together the mobility and independence of diesel power with the efficiency of electric drive
Working principle: The crusher (whether jaw, cone, or impact) in a hybrid setup is the same mechanically as its purely diesel-hydraulic counterpart, but the power transmission differs. Instead of running the crusher directly via hydraulic pumps off a diesel engine, the hybrid design uses an onboard generator to supply electricity to electric motors on the crusher and conveyors. Many hybrid models also have the ability to plug into mains electricity or a site generator. This means on a site with grid power, the entire unit can run 100% electric, with zero diesel usage . If no grid power is available, the diesel engine on the machine powers the generator to drive the electric motors. Some hybrids are called “dual-power” crushers for this reason. The crucial advantage is that electric motors can deliver torque very efficiently and only draw power as needed, whereas diesel-hydraulic systems run the engine at high RPM constantly to provide pressure. By combining the two, hybrid crushers optimize energy use: the diesel runs at its most efficient constant RPM, and peak loads are handled by the electric system’s ability to surge power quickly
Key advantages: The primary benefit for buyers is lower operating costs and fuel consumption. Electric drives are generally more efficient than hydraulic drives; they waste less energy as heat and can be precisely controlled Many hybrid mobile crushers report significantly reduced diesel usage – in some cases 30% or more fuel savings – compared to traditional diesel-hydraulic models, especially if crushers are run consistently at high load. Additionally, maintenance costs can be lower: electric motors and generators usually require less servicing than complex hydraulic systems (fewer hydraulic hoses, fluids, and pumps to maintain) The diesel engine in a hybrid often experiences less stress (running at steady optimal load) and thus can have a longer service life with reduced maintenance frequency Another big advantage is emissions and environmental compliance. Hybrid crushers produce lower exhaust emissions and can even run emission-free when plugged into electric power This is a huge benefit for urban job sites or strict environmental zones, where running a large diesel engine continuously might not be allowed or could require special permits. Some governments and local authorities also incentivize the use of electric or hybrid equipment (grants, tax breaks, or easier project approval), which can make hybrid models financially attractive in the long run . From the perspective of the job site, hybrids also tend to run quieter, especially in electric mode, improving conditions for workers and neighbors.
Considerations: Hybrid mobile crushers typically come at a higher initial purchase price due to the added complexity of dual power systems and generators . Therefore, a buyer should weigh the up-front cost against the anticipated savings in fuel and maintenance. For contractors who move frequently between sites, the ability to plug into grid power can be a game-changer; on remote sites without electricity, the hybrid still operates like a normal diesel machine. Mobility and performance of hybrid models are on par with their conventional counterparts – you do not sacrifice crushing capacity or portability by going hybrid. For example, a hybrid jaw crusher will have the same feed size capacity and throughput as the equivalent purely diesel model, it will just burn less fuel per ton. One thing to consider is training and support: hybrid systems involve electrical components that may require different maintenance skills (high-voltage training for technicians, etc.), and not all dealers may have equal expertise in them yet. However, most major manufacturers (Terex Finlay, Kleemann, Metso, Powerscreen, etc.) now offer or are moving toward hybrid ranges across jaw, cone, and impact lines. These models often come with the latest automation features as well – remote monitoring, telematics, and software to optimize the diesel-electric interplay (for instance, auto-start/stop systems, power monitoring, etc.).
In summary, hybrid crushers present an eco-friendly, cost-efficient option for mobile crushing. They particularly make sense for buyers with long-term projects where fuel savings will accumulate, or for those working in areas where noise and emissions are tightly regulated. With hybrids, you’re investing more initially to reap operational savings and future-proof your equipment against rising fuel costs or environmental restrictions.
Comparison Chart of Mobile Crusher Types
To clarify the differences between these crusher types, the following table provides a side-by-side comparison of key technical parameters and features. This includes typical input feed size range, throughput capacity, power requirements, mobility considerations, and maintenance needs for each type of mobile crusher:
Crusher Type | Typical Max Feed Size | Typical Capacity Range | Power Consumption / Drive | Mobility | Maintenance Needs |
---|---|---|---|---|---|
Jaw Crusher | Largest of all: often up to ~1000–1200 mm feed (very large models can handle even bigger) | ||||
Jaw Crusher VS Cone Crusher: 9 Key Differences | Moderate to High. Mobile jaw plants range from ~50 TPH for small units to 500+ TPH for larger models (biggest jaw units ~1000+ TPH) | ||||
Jaw Crusher VS Cone Crusher: 9 Key Differences] | Generally lower power demand per ton. Uses a large diesel engine (200–400 kW typical) but runs at lower RPM; efficient energy use due to flywheel. Less HP required compared to impact for similar output | Highly mobile (track or wheel-mounted). Often used as primary crusher that can be moved to follow the excavation or quarry face. Some very large jaws are semi-mobile due to weight, but most track-jaws can be relocated readily on-site. | Low to moderate maintenance. Simple design with few wear parts. Jaw plates need replacement or rotation periodically (interval depends on material abrasiveness). Easy access for maintenance; typically requires less frequent attention than impactors Lubrication of bearings and toggle checks are routine. | ||
Impact Crusher (HSI) | Large for an impactor: typically up to ~600–800 mm for primary HSIs (smaller HSIs used in secondary stages may take ~300–400 mm feed). | High. Capable of 100–600 TPH depending on rotor size and power. Primary HSIs in limestone can exceed 500 TPH; smaller units for recycling are in the 100–300 TPH range. | High power requirement to sustain rotor speed. Diesel engine (or electric motor) often in the 250–500 kW range for bigger HSIs. Consumes more fuel per ton when crushing hard rock (due to energy lost as heat, noise). However, very effective reduction per pass. | Highly mobile (track-mounted common). Suited for both quarry use and on-site recycling projects. Can be moved and set up quickly. Usually self-contained with onboard diesel (or genset for hybrid). | High maintenance relative to jaw/cone. Blow bars and impact plates wear faster, especially on abrasive rock – may need replacement frequently (e.g., blow bars can last weeks or months based on material). Regular inspections required; downtime to flip or change bars is part of operation. Dust and fines buildup should be managed. On the plus side, wear part changes are generally straightforward, and maintenance can be planned if monitoring wear. |
Impact Crusher (VSI) | Smaller feed: typically up to 50–150 mm depending on VSI design. (Requires pre-crushed material; not suitable for large unbroken rocks.) | Moderate. 50–300 TPH common for mobile VSI units. They are often fed with already reduced material, so throughput is on finer products. Some high-end VSI can approach 400 TPH with ideal conditions. | Moderate to high power need. VSI rotors spin very fast (~1000-2000 rpm); motors ~150–400 kW are common. Power consumption per ton can be high if making very fine sand (due to the energy to create fines), but if fed with proper size, they operate efficiently. Often powered by onboard diesel generator or electric motor. | Highly mobile (track or wheel). Often used as part of a multi-stage mobile setup (e.g., after a cone or as part of an integrated mobile plant with a screen). Can be moved on-site. Some VSIs are also available in stationary or portable configurations for asphalt plants. | Moderate maintenance, but critical to monitor. Wear parts include rotor tips, anvils or rock shelf, and wear plates – these must be inspected as they can wear unevenly. Abrasive sand production can wear parts quickly, but parts are usually modular for change. Keeping a consistent feed is important to avoid imbalance. Maintenance involves checking the rotor (for clogging or wear) and replacing wear parts typically more often than a cone but less often than an HSI in similar service. |
Cone Crusher | Medium: generally ≤ 300–400 mm for secondary cones (primary gyratory cones can take ~1000mm but those are usually static or very large semi-mobile units) | ||||
Jaw Crusher VS Cone Crusher: 9 Key Differences] | |||||
Jaw Crusher VS Cone Crusher: 9 Key Differences] Mobile cones usually follow a primary, so feed is pre-crushed. | High. 100–500+ TPH for most mobile cone plants. Larger models (with 300-500 kW motors) can output 600+ TPH in ideal conditions. Cones shine in continuous high-volume production and can be scaled to very large capacities in fixed plants | ||||
Jaw Crusher VS Cone Crusher: 9 Key Differences] | High power drive needed to achieve and maintain throughput. Typical mobile cone uses 200–400 kW drive (either direct electric or diesel-hydraulic). Steady power draw when “choke-fed” (which is ideal for efficiency and product quality). Energy per ton is low compared to impact, due to the interparticle crushing – good fuel economy when properly fed | Highly mobile on tracks (common in secondary/tertiary roles). Often part of a multi-stage setup (following a jaw). Track cones can travel to sites and reposition easily, though they generally stay put longer at a central location in the pit after primary crushing. Also available as wheel portable units for highway transport between sites. | Moderate maintenance. Wear liners (mantle and concave) last a significant time but still need regular monitoring; changes are typically after tens of thousands of tons, depending on rock hardness. More complex than jaw (hydraulics, lubrication, automation systems) but well-engineered for durability. Routine maintenance includes monitoring liner wear (automated systems help), keeping oil clean/cool, and ensuring the feed is not too wet or segregated (to prevent undue wear). Overall maintenance cost is lower than impact crushers for hard materials and downtime for liner changes can be planned with predictive maintenance. | ||
Hybrid (Diesel-Electric) Model | Varies – A hybrid can be a jaw, cone, or impact crusher, so the feed size depends on that crusher type. Hybrids don’t alter feed capacity inherently; e.g., a hybrid jaw accepts the same ~1000mm feed as the diesel-only version. | Same as equivalent conventional model – The crushing capacity is not compromised by the drive type. A hybrid jaw or cone will produce the same TPH; the difference is in how the machine is powered. | Lower fuel consumption due to electric efficiency. Equipped with a diesel engine (to generate power) often similar in size to conventional units, but optimally loaded. Electric motors drive the crusher and conveyors with high efficiency ([Mobile Hybrid Crushers | Full-Electric Operation | RUBBLE MASTER] If plugged into grid power, diesel use is zero. Operating cost per ton is reduced (often 20–30% less fuel) and the diesel engine runs at steady optimal RPM (improving longevity). |
Table: Comparison of mobile crusher types by feed size, capacity, power, mobility, and maintenance. Each type has unique advantages that suit different applications and buyer priorities.
How to Choose the Right Machine
Selecting the best mobile crusher (and screening setup) for your operation requires careful consideration of several factors. Here are key buyer considerations and expert tips to guide the decision:
- Material Type and Hardness: Evaluate the material you will be crushing. For very hard or abrasive rock (e.g. granite, basalt), a jaw crusher (for primary breaking) paired with a cone crusher is often the most durable and cost-effective choice For softer stone or recycled materials like concrete and asphalt, an impact crusher can be ideal because it achieves good reduction and shape in a single stage If your material is brittle (like limestone) or less abrasive, you can use impactors to simplify the process. Always match the crusher to the material’s hardness and abrasiveness to balance wear cost against productivity.
- Feed Size and Desired Output: The maximum size of raw material dictates the primary crusher choice. Large boulders or chunks (>600mm) will usually require a mobile jaw crusher as the primary unit (or a very large HSI if the rock is soft), since jaws have the widest feed openings Conversely, if your input material is already small (e.g. coming from a previous stage or a stockpile of broken material), you might skip straight to a cone or impactor. Also, define the required product size and shape. If you need fine or sand-like output, plan for a VSI or a fine cone in your lineup. If a particular shape (cubical, with minimal flats or slivers) is needed (common in concrete aggregate), an impact crusher or adding a VSI in the process will be beneficial On the other hand, if your output can be a bit coarser or will be reprocessed, a jaw+cone arrangement might suffice. Essentially, choose a crusher that can accept your feed in one end and give your desired product at the other, possibly in stages.
- Throughput Capacity Requirements: Determine how many tons per hour (TPH) you need to process and consider any future scaling. Each crusher type comes in various sizes – ensure the model you select can meet your peak production needs. Jaw and cone crushers generally handle higher continuous throughput (and larger volumes) better, whereas impact crushers are sometimes chosen for their high reduction but might require screening to meet capacity on spec material If you anticipate needing above ~500 TPH, you will likely be looking at jaw+cone combinations or multiple units. Always factor in some buffer; running a machine constantly at 100% of its rated capacity can increase wear. It might be wise to choose a crusher that exceeds your required capacity slightly, ensuring it can run at ~80-90% capacity for longevity.
- Mobility and Site Conditions: Consider how and where the machine will be used. Track-mounted mobile crushers are excellent for jobs that require frequent moving (e.g., following an excavation site or moving between short-term projects) If you’ll move the crusher only occasionally between sites, you might also consider a wheeled (portable) unit, which can be towed by a truck – these can be more cost-effective but take a bit longer to set up compared to track units . Think about terrain: tracks handle rough, uneven ground better and can self-propel into position. Also, assess the space on site – mobile crushers vary in footprint. Ensure the unit (plus any attached screen or discharge conveyors) fits your space and can be operated safely. If working in urban or densely populated areas, compact mobile crushers or those with noise-and-dust suppression can be valuable. Additionally, consider the availability of power: if your site has access to electrical power or if you operate in enclosed environments, a hybrid crusher that can plug in might be advantageous for zero-emission, quiet operation
- Operating Costs (Fuel and Wear): Analyze your cost priorities – initial cost vs operating cost. Impactors typically cost less to purchase upfront than cones of similar capacity, but wear parts and fuel may cost more over time Cones and jaws might have higher initial price tags, but their long-term wear part life is usually better, meaning lower ongoing replacement costs If fuel efficiency is a big concern (for example, if diesel is expensive in your region or you plan to run the machine continuously), consider either a jaw crusher (lower horsepower per ton) or a hybrid/diesel-electric model which can significantly cut fuel usage Always request information on specific fuel consumption (liters or gallons per ton) from the manufacturer or dealer – it can vary widely and dramatically impacts operating cost. If possible, estimate wear part consumption: for instance, blow bar life in an impact vs liner life in a cone for your material, and price those parts. Some dealers will provide cost-per-ton wear estimates based on similar applications. This will help you project the total cost of ownership over a few years.
- Maintenance and Durability: All crushers require maintenance, but your team’s capability and the planned downtime window matter. Jaw crushers are relatively straightforward – if you prefer a machine that your mechanics can work on easily and has fewer computerized components, a jaw or simple HSI might fit the bill. Impact crushers will need more frequent attention (checking blow bars, clearing any clogs, etc.), so ensure you have a plan for spare parts and labor. Cone crushers have more complex components (hydraulics, automated settings) – they reward you with long liner life, but you need to stick to the maintenance schedule (lubrication, filter changes, etc.) to avoid costly breakdowns. If your project is in a remote area with limited access to service, you might lean towards the most robust, simplest solution (often a jaw crusher) as your primary workhorse, since it can often run under less-than-ideal conditions and still keep going . Also, check the build quality: look for features like wear-resistant steel, good guarding, dust suppression systems, and ease-of-access for maintenance on the models you consider. A machine designed with quick part replacement (e.g., hydraulic chamber opening for impactors or wedge systems for jaw die change) will reduce your downtime.
- Automation and Technology Features: Modern mobile crushers come with a range of smart features that can improve safety and efficiency. Evaluate which features are important for you. Some useful ones include:
- PLC or Computer Control Systems: These can automate feeder speed, adjust crusher settings, and even auto-regulate based on load, ensuring optimal throughput without manual intervention.
- Level Sensors and Auto-Feeders: Many crushers have sensors in the hopper or on the crusher that detect material level and can adjust the feeder or conveyor to prevent overfilling or starvation. For example, maintaining a “choke feed” on a cone crusher is crucial for consistent operation – sensor-driven feeders can help achieve this.
- Telediagnostics and Telematics: Systems like remote monitoring (often via cellular or satellite link) allow you to track machine performance (tons crushed, fuel used, engine hours) and receive alerts for maintenance or faults. This is great for fleet management or if you want to ensure the crusher is being used optimally. The Finlay T-Link or similar systems from other brands provide such capabilities as standard on many new models
- Safety Features: Look for things like camera systems for viewing the feed hopper from the ground, automated shut-offs if a blockage is detected, hydraulic release systems for uncrushable objects (especially on cone crushers to release tramp metal), and good walkway/access designs for maintenance. These not only protect your crew but also the machine from damage.
- Hybrid Power Options: As discussed, if you foresee stricter environmental rules or want the flexibility of running electric, opting for a model with hybrid capability might be wise for “future-proofing”. Even if you run on diesel now, having the option to plug in could increase resale value as demand for low-emission equipment rises.
- After-Sales Support and Parts Availability: This is an often overlooked but crucial factor. No matter how good a crusher is, timely support and spare parts supply will determine your uptime. When choosing a brand or dealer, consider their network – do they have local service technicians? Are common wear parts and spares stocked in your region? Check if they offer training for your operators and mechanics. A machine with fancy tech is only beneficial if your team knows how to use it and fix minor issues. Speak to other users of the same equipment if possible, or ask the manufacturer for references. A slightly more expensive machine might be worth it if it comes with strong service commitments and lower downtime.
By weighing all these factors – from the nature of your material and production goals to the practicalities of maintenance and support – you can zero in on the mobile crusher (or crushing circuit) that best fits your needs. It’s often beneficial to consult with application specialists or engineers from the equipment manufacturer, as they can simulate or reference similar setups and help refine your choice. In many cases, the optimal solution may be a combination of crushers (e.g., a primary jaw plus a secondary cone, or a primary impactor plus a VSI for fines) along with mobile screens to achieve the desired output.
Conclusion
Mobile crushing and screening machines have become indispensable in modern aggregate production and recycling, thanks to their flexibility, high performance, and on-site processing capabilities. Understanding the differences between jaw, impact, cone, and hybrid crushers is key to making an informed investment. To recap: jaw crushers offer a heavy-duty solution for large, hard feed and are valued for their durability and simplicity; impact crushers (HSI) provide high reduction and excellent product shape for softer materials and recycling applications, while vertical shaft impactors (VSI) excel in fine crushing and shaping tasks. Cone crushers deliver high throughput and efficient reduction for hard rock with lower wear costs, making them ideal for secondary/tertiary crushing in high-volume operations. Meanwhile, hybrid models represent the latest evolution, combining diesel and electric power for lower operating costs and environmental impact
Each crusher type has its own strengths: there is no one-size-fits-all crusher. The best choice depends on the material characteristics, production requirements, and operational priorities of the buyer. By considering technical specifications like feed size capacity, output gradation, power consumption, and maintenance needs – alongside practical factors like mobility, site conditions, and automation features – buyers can identify the machine (or combination of machines) that will deliver the greatest value. Remember that a well-chosen mobile crusher not only maximizes production but also minimizes downtime and cost over its lifetime
In closing, investing the time to assess your crushing needs and doing a thorough comparison will pay off. Leverage this guide and insights from industry experts to make a sound decision. With the right mobile crushing and screening equipment in place, you’ll benefit from efficient on-site material processing, reduced haulage costs, and the flexibility to adapt to changing project demands – an edge that can boost both productivity and profitability in your operations. Happy crushing!