Modular Impact Crushers: Revolutionizing Soft Rock Crushing
Release time: 2025-03-20
When it comes to processing soft rocks like limestone, gypsum, or shale, efficiency and precision are paramount. Modular impact crushers have emerged as a standout solution, offering a blend of adaptability, performance, and cost-effectiveness that’s hard to beat. Designed with flexibility in mind, these machines are transforming how industries handle soft rock crushing, from construction to mining.
Let’s dive into what makes modular impact crushers so effective, how they operate, and where they shine in real-world applications.
The Power Behind Modular Impact Crushers
At their core, modular impact crushers are engineered to break down materials using high-speed impact forces rather than compression. This approach is particularly suited for soft rocks, which can crumble under excessive pressure from other crusher types, producing unwanted fines. The modular design adds another layer of ingenuity—components can be easily assembled, disassembled, or reconfigured, making these crushers ideal for projects requiring mobility or quick setup.

Most modular impact crushers fall into the Horizontal Shaft Impactor (HSI) category, which excels at handling soft to medium-hard materials. Unlike their Vertical Shaft Impactor (VSI) counterparts, which are better for shaping or finer crushing, HSIs deliver the raw power needed to process soft rock efficiently.
Curious about how these machines stack up against other options? Check out our detailed comparison of jaw crushers。vs. impact crushers to see the differences in action.
Why Soft Rock Crushing Thrives with Modular Impact Crushers
Soft rocks like limestone and dolomite have unique properties—less abrasive but prone to over-crushing if mishandled. Modular impact crushers are tailor-made for these materials, offering several key advantages:
- Precision Crushing: The impact mechanism ensures a clean break, producing cubical aggregates perfect for construction applications like concrete or asphalt.
- High Throughput: Capable of reducing large soft rock pieces into usable sizes in one pass, these crushers save time and boost productivity.
- Low Wear: Softer materials mean less strain on components, reducing maintenance costs compared to crushing harder rocks like granite.
- Portability: The modular setup allows operators to move or adjust the crusher as needed, a boon for multi-site operations.
For more insights into crusher versatility, explore our guide on mobile crushing solutions.
Breaking Down the Crushing Process
How do these machines turn raw soft rock into valuable aggregates? Here’s a look at the mechanics:
- Feed Intake: Soft rock enters the crusher chamber via a hopper or conveyor.
- Rotor Impact: A high-speed rotor, equipped with blow bars, strikes the material, shattering it on contact.
- Secondary Breakage: The fragmented rock then collides with anvils or aprons, further reducing its size.
- Output Control: Adjustable settings, like rotor speed or gap width, allow operators to fine-tune the final product size.
This process ensures consistent results without over-pulverizing the material—a common issue with compression-based crushers when handling soft rock.
Applications That Showcase Their Strength
Modular impact crushers aren’t just theoretical marvels; they’re workhorses in industries worldwide. Here’s where they make an impact:
- Mining: Efficiently crushing soft ores like limestone for downstream processing.
- Construction: Producing high-quality aggregates for roads, buildings, and infrastructure projects.
- Recycling: Breaking down soft concrete or asphalt for reuse in sustainable projects.
Their ability to adapt to different environments makes them a favorite for temporary setups or urban projects. Want proof? See how they perform in our case study on efficient crushing solutions for urban projects.
Standing Out Against Other Crushers
Not all crushers are created equal, especially when soft rock is on the table. Here’s how modular impact crushers compare:
- Jaw Crushers: Better for hard rock, jaw crushers can over-crush soft materials, leading to excessive dust and fines.
- Cone Crushers: Designed for tougher rocks, they’re less efficient and more costly for soft rock applications.
- Hammer Mills: While also impact-based, they lack the modularity and precision of modern impact crushers.
For a broader look at crusher options, visit our breakdown of the different types of stone crushers.
Key Features to Look For
When selecting a modular impact crusher for soft rock, a few standout features can make all the difference:
- Adjustable Output: Control over rotor speed and gap settings ensures the right aggregate size for your needs.
- Robust Build: Even for soft rock, durable blow bars and anvils extend the machine’s lifespan.
- Mobility Options: Track-mounted models enhance portability—perfect for shifting job sites.
Need help picking the right equipment? Our guide on how to choose the best crusher for your project offers practical tips.
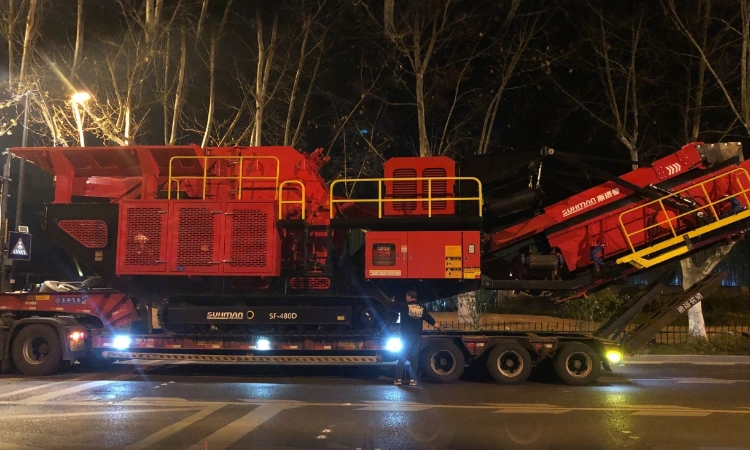
Modular impact crushers are more than just machines—they’re a strategic advantage for anyone working with soft rock. Their blend of efficiency, adaptability, and precision continues to redefine crushing standards across industries. Whether you’re scaling up production or tackling a new site, these crushers deliver results that speak for themselves.